About
What does this tool do?
The MARS software tool allows for the design of the rail-wheel system of Stacker Cranes (SC) according to the standard EN 13001-3-3. It automatically computes the proofs of static and fatigue strength for both wheels as well as the rail based on the input parameters provided by the user. When computing the proof of fatigue strength it is necessery to compute the contact force spectrum factor kc and the relative number of rolling contacts vc. Those two parameters are computed by the tool based on simulation experiments conducted within the MARS project. The tool computes vc based on an average travelled distance per cycle which depends also on the chosen cycle mode and rack length. For computing kc the tool uses a Gaussian Process (GP) prediction model.
How to use this tool
Using this tool follows a very simple workflow:
- If you don't have the input file yet you can download it here
- Set the parameters in the input file for as many configurations as you like. The file gives you hints on each parameter in case you are unsure about it
- Choose an SC configuration (1 Mast or 2 Masts) and upload input file
- For the 1 Mast SCs there are two configurations (see figure below): moving direction right and left
- Choose a computation mode: Proof (computes the proofs for given configurations) or Min. Diameter (computes for given configuration min. diameter so that all proofs are fullfilled)
- Start computation, which will take a couple of seconds
- After computation download result file
- Possible errors will be displayed
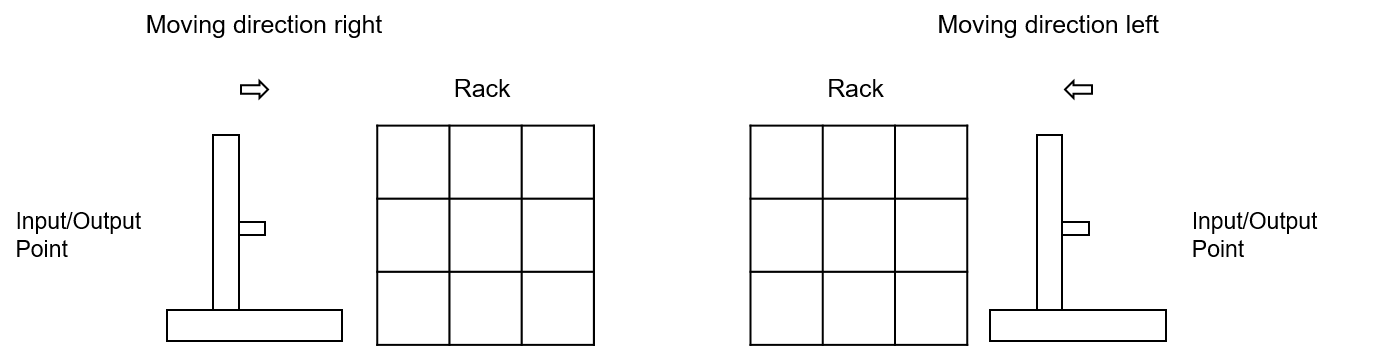
Input file structure
The input file consists of 5 sheets containing information that is needed for computation.
Material sheets
There are two material sheets: one for the wheels and one for the rail. The material sheets contain all possible materials for the wheels and the rail which are sepcified by their parameters. By default the material sheets contain the standard materials from the EN 13001-3-3's appendix. New materials may be added by simply adding a new row.
Geometry sheets
Similarly to the material sheets there are sheets containing the possible wheel and rail geometries.
Input Variables
This is the main sheet. Here you can set all parameters that define the SCs you'd like to design a rail-wheel system for. There are two groups of input parameters.
- The general parameters used in EN 13001-3-3
- Parameters describing the SC configuration. These parameters are needed for predicting kc and vc
- Mass per height/length [kg/m]: this only considers the mast's or traverse's own mass, not additional masses
- Height/length [m]
- Total mass
Result file structure
The result file will have two sheets.
Summary
- For computation mode "Min. Diameter": min. diameter that fullfilled all proofs. (NaN means that there was no wheel geometry for which all proofs were fulfilled)
- Results of static and fatigue proof for both wheels and rail (True=Fulfilled, False=Not fulfilled)
- Input data of each configuration
Results
- For computation mode "Min. Diameter": min. diameter that fulfilled all proofs
- Detailed results of static and fatigue proof for both wheels and rail
- Input data of each configuration
Type of errors that can occur
There are three kind of errors that can occur during computation that the tool will tell you about.
A fatal error means that the input file was broken. A possible cause for this would be that the input file that was uploaded didn't have all sheets required for computation or that a variable was missing (e.g. a raw or column was deleted). When a fatal error occurs there is no result file generated. Please redownload the input file an run your computation again.
Regular errors happen when one or multiple configurations in the input file contain variables that have the wrong type or an invalid value. These configuration are deleted and the remaining configurations are computed. You will be informed when input configurations had errors and were deleted.
Warnings are displayed when there were configurations in the input file that contained unexpected but valid values. This means that the tool was able to compute these configurations but one or more variables had values that were outside the expected interval. You should then check the values which you got a warning about. If you are sure about your values you can ignore these warnings.
How to interpret the results
As mentioned above the tool uses a Gaussian Process model to predict kc which is then used for computing the proof of fatigue strength. Additionally to making a prediction GPs compute the uncertainty of the prediction in terms of a confidence interval. A large confidence interval means that the GP is uncertain about its prediction. A small confidence interval corresponds to a confident prediction. Besides the GP's prediction the MARS software tool also uses the upper bound of the confidence interval for further computation. This means that there are two results of kc: a prediction and the upper bound of the confidence interval which represents a "worst case scenario". The corresponding results are labelled "prediction" and "upper". Besides kc itself all parameters that are computed from it have a label "prediction" and "upper". These parameters are:
- The contact force history parameter sc
- The limit force for fatigue strength Frd,f
- The proof of fatigue strength's result